Thanks to a partnership with a Northern Irish company, we’ve found a cost-efficient way to ensure that 100% of our wind turbine blades can be sustainably recycled – and turned into new, useful resources.
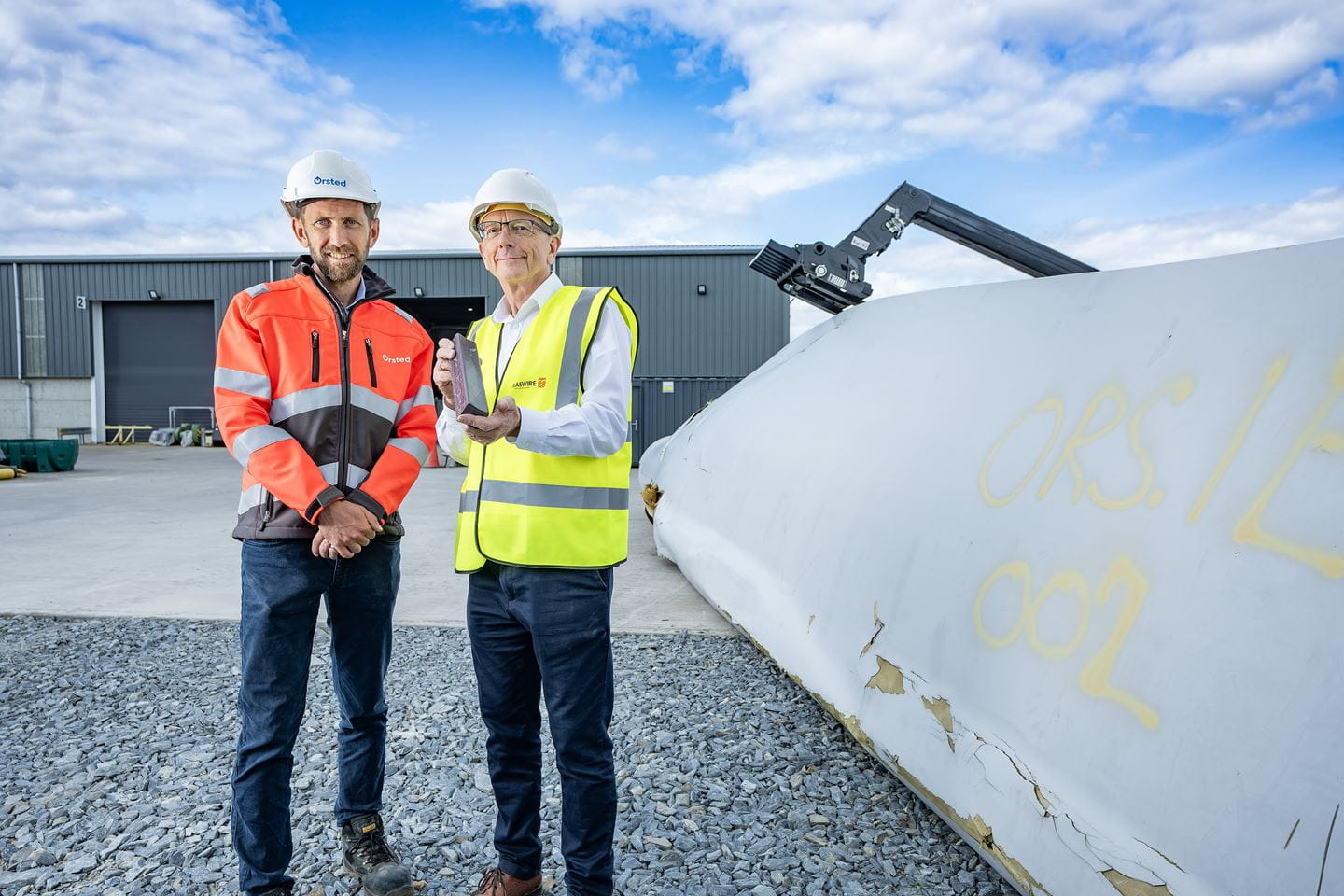
The challenge
Up until now, turbine blades have been notoriously hard to recycle. While 85-95% of a wind turbine can be recycled, the blades have presented a particular challenge.
Designed to be lightweight, yet highly durable, blades are usually made of fibreglass or carbon fibre and are held together with resin. This makes them particularly hard to break down for recycling. As a result, most decommissioned blades end up in landfills.
With wind power expected to expand exponentially in the coming decades, the issue of how to dispose of used blades will only become more acute.
As renewable energy leaders, at Ørsted we have a responsibility to help find innovative solutions to the challenge of recycling used blades.
In 2021 we announced our commitment to either reuse, recycle, or recover all of the wind turbine blades in our global portfolio of onshore and offshore wind farms upon decommissioning.
A scalable success
With a growing portfolio of 378 MW of onshore wind assets across the island of Ireland, we are particularly pleased about the success of our recent pilot project with Plaswire, a County Armagh based company.
The pilot project saw three blades from a decommissioned turbine at Ørsted’s Owenreagh Wind Farm in County Tyrone successfully recycled.
The blades were first cleaned and shredded, then granulated and finally utilised in Plaswire's smart RX Polymer, a material typically used in the construction industry.
During the pilot, Plaswire recycled 100% of Ørsted’s used turbine blades, ensuring that valuable resources are turned into new products that can substitute materials such as virgin plastics, steel, and concrete instead of simply going to waste.
The cost-efficient and scalable method developed by the Ørsted - Plaswire partnership is promising for the wider wind energy industry.
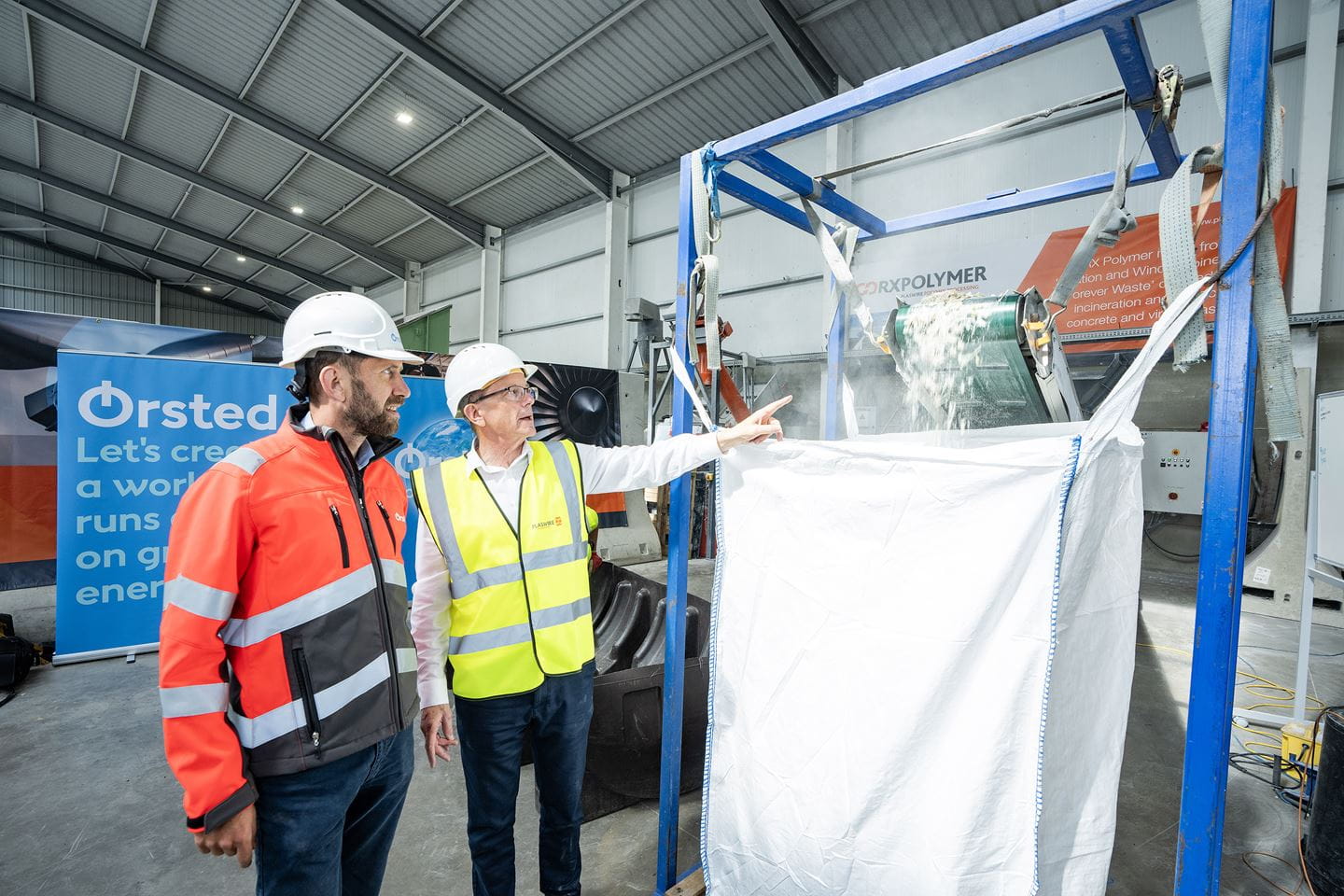
Moving towards a more circular practice
“As some of our onshore fleet approach their end of life, we are excited to have found a local partner, who has the technology to break down our turbine blades and remould the materials into new, durable RX polymer,” said Ray O’Connell, Director of Operations at Ørsted UK & Ireland.
O’Connell said he was particularly excited that the recycling could all be done right on the island of Ireland – removing the additional carbon costs associated with international shipping.
“Plaswire is helping us move towards more circular decommissioning practices where we strive to turn waste into new, useful resources,” he added.
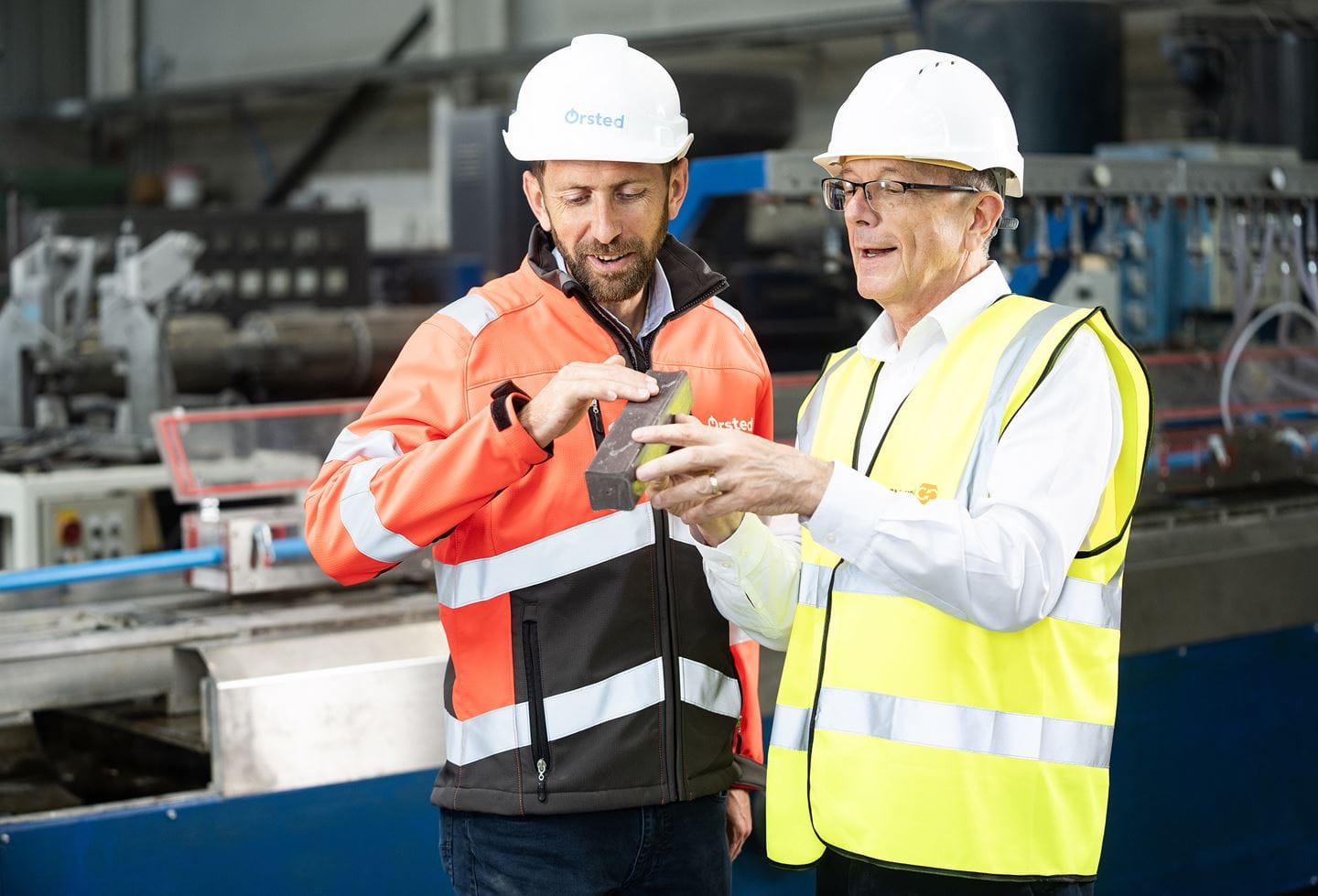
Andrew Billingsley, CEO of Plaswire, said he was pleased that his company was doing its part to help tackle the global industry challenge.
“The sustainable recycling of wind turbine blades is a global challenge and Plaswire is pleased to collaborate with Ørsted to develop a scalable solution for the wind industry to avoid blades ending up in landfill.”
In the coming months Ørsted will continuing to mature the partnership with Plaswire with a focus on scaling the technology in preparation for more decommissioning projects.